中國冶金報報道組
報道組成員:劉加軍、徐可可、王志、賈林海、藍義高
本篇執筆:賈林海
利用AI(人工智能)識別鋼坯進出爐情況、依托5G技術連接生產全要素、佩戴VR(虛擬現實)設備進行檢修……走進江蘇永鋼集團有限公司(以下簡稱永鋼),智慧煉鐵、智慧煉鋼、智慧軋鋼、智慧物流,智造場景遍地開花。
近年來,永鋼精準把握數字經濟新賽道,推動互聯網、大數據等新興技術與鋼鐵主業深度融合,在數智化轉型方面走在行業前列。過去的一年里,永鋼累計獲得國家級、省級數智能化榮譽19項。
日前,《中國冶金報》記者一行走進永鋼,探尋其以智慧制造賦能鋼鐵高質量發展的奧秘。

圖為永鋼廠區
當“示范”,靠什么?
2023年10月份,工信部公示了2023年度智能制造示范工廠擬揭榜單位,永鋼特種合金棒材智能制造示范工廠入選,成為永鋼數字化轉型工作邁上新臺階的有力見證。
成績遠不止于此。截至目前,永鋼建成1個國家級智能制造示范工廠、3個國家級5G全連接工廠、2個江蘇省智能制造示范工廠、1個江蘇省互聯網標桿工廠、7個江蘇省智能制造示范車間,獲評為工信部大數據應用試點示范項目、江蘇省“兩化融合”示范企業……
如此多的“示范”傍身,永鋼憑借什么?在永鋼特種合金棒材智能制造示范工廠,《中國冶金報》記者找到了答案。

圖為永鋼數字孿生工廠
“叮咚!”永鋼云商平臺頁面上彈出一個新訂單,有客戶想要采購一批特種合金棒材。隨即,特種合金棒材智能制造示范工廠便開始運轉,根據客戶需求制訂個性化生產方案,智能生成原材料采購、生產排期計劃、標準化工藝管理……客戶只需一鍵下單,就能量身定制所需產品,“要煉什么樣的鋼,客戶說了算”。
2020年,永鋼啟動特種合金棒材智能制造示范工廠項目,以實現生產過程全流程一體化管控。
“這個項目涵蓋數十個應用場景,串聯起質量管控、計劃調度、生產作業、設備管理、能源管理、安全管理、環保管理等十余項業務環節。”永鋼黨委書記、總裁吳毅告訴《中國冶金報》記者。
當特種合金棒材開啟生產之路,“沿途”所有車間的智能化平臺就已經準備就緒,智慧料場、煉鐵、煉鋼、軋鋼,智能精整熱處理、精準配送……智造統領鋼鐵生產全局。
“以質量管控為例,以往,鋼坯需要人工測量和肉眼觀察產品質量,這對崗位人員的技能、經驗水平有著較高要求,檢驗結果的實時性、客觀性、樣本覆蓋面等無法全面滿足精益生產的需要。”永鋼副總裁程勇說道。
如今,特種合金棒材智能制造示范工廠借助5G、AI視覺分析等數字技術,通過低倍組織AI自動檢測等子系統,可以精準、智能檢測產品質量,實現檢測效率和產品質量“雙提升”。

各類專利
僅在這一生產環節中,永鋼就形成了《一種基于機器視覺的鋼材低倍數字化檢測方法》《一種鋼材低倍缺陷組織自動成像及檢測分析裝置》等13項專利。
智慧管控還體現在綠色生產上。通過大數據技術集成的碳排放監測平臺、數據中臺等,永鋼可以實時統計燒結、球團、煉鐵、煉鋼等主要工序的碳排放數據,并同步監控焦、煤、電等30多類能源使用,為生產工序優化提供數據分析支撐,助力全流程降碳3%。
“在整個項目中,我們導入了AI模型、時空融合數字孿生模型、工藝及研發仿真模型、業務流程模型、機理模型、數據算法模型、邊緣側控制模型等414個工業模型,參與現場過程控制的計算與反饋。”永鋼數字化部門相關負責人介紹。
據統計,特種合金棒材智能制造示范工廠項目讓生產效率、能源利用率提高了12%以上。同時,通過打通“冶煉—連鑄—軋制—熱處理”等工藝流程,產品研發周期也縮短了近40%。
如今在永鋼,智能化浪潮從線上向線下奔涌,一場場數字技術與鋼鐵產業的化學反應正在加速上演。
用AI慧眼識“鋼”
近年來,AI技術飛速發展,在重塑人類生活方式的同時,也深刻改變了工業生產,AI助力下的鋼鐵自動化、數字化、智能化生產成為發展新趨勢。
在推動AI賦能工業生產方面,永鋼也做出了不俗的成績。
“以前,在鋼坯進行軋制前,需要將其送入加熱爐加熱。在鋼坯出入爐部分通常需要人工觀察鋼坯位置、形狀等,以保證鋼坯正常出入加熱爐。”程勇告訴《中國冶金報》記者,“靠工人眼睛長時間盯著,強度很大,如果沒能及時發現鋼坯料彎、料斜等情況,就會影響加熱爐正常進出鋼節奏,導致生產誤時。”
為解決這一問題,2022年7月份,永鋼數字創新部、普鋼棒材分廠聯動上線了自動裝出爐控制優化信息化改造項目。通過AI視覺技術,替代人工對出爐鋼坯的異常情況加以識別,為現場自動化控制系統提供進出鋼輔助控制信號。
“我們不斷為AI機器視覺豐富樣本數據,讓AI深度學習、訓練、調整模型,最終優化得到最佳模型。”永鋼數字化部門相關負責人介紹,在生產過程中,AI會將鋼坯進出爐識別結果輸出給自動化控制程序,鋼坯進出爐到位時,控制程序自動進行下一步操作;鋼坯進出爐異常時,控制程序會發出預警,提醒工作人員及時人工干預。
不僅如此,通過AI視覺技術,技術人員還能分析信號并記錄,回溯異常發生時的情況,找到原因并生成數據樣本建入AI模型,進一步優化模型效果,提高生產效率。
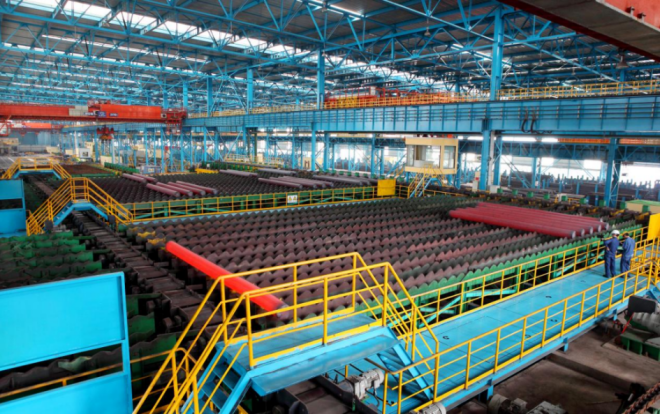
圖為永鋼智能車間
AI,讓永鋼更聰明地煉鋼。目前,永鋼普鋼棒材分廠車間自動裝出爐輔助控制已平穩運行,出爐輥道鋼坯和爐內鋼坯料識別準確率都達到95%以上,不僅縮短了鋼坯進出爐用時,提高了單位時間內鋼坯處理數量,穩定了鋼坯進出爐節奏,還實現了精準測控,進一步保證了產品軋制質量。
“接下來,我們將以生產需求為導向,持續推動AI視覺與智能制造深度融合,在現場管理、身份識別、產品數量及缺陷檢測等方面做出更多可行性嘗試。”吳毅表示。
5G點亮未來鋼廠
2023年7月份,江蘇省蘇州市工信局發布了2023年度蘇州市5G全連接工廠項目公示名單,永鋼固廢循環利用5G全連接工廠項目入圍。
5G全連接工廠是指利用以5G為代表的新一代信息通信技術集成,打造新型工業互聯網基礎設施,新建或改造生產現場,形成生產單元廣泛連接、信息(IT)運營(OT)深度融合、數據要素充分利用、創新應用高效賦能的先進工廠。
近年來,永鋼著力推動“5G+制造”,在自動化、信息化、數字化、智能化方面加強建設,使生產現場變得井然有序、智能高效。

圖為永鋼固廢利用智能工廠
走進永鋼固廢循環利用5G工廠,在冶金塵泥加工車間,《中國冶金報》看到操作員正坐在中控室,遠程操控車間設備運行,了解生產進程,觀察設備運行狀態、環保檢測等信息。
通過應用5G技術,永鋼固廢循環利用5G工廠不僅有效提高了生產效率、降低了生產成本、提升了安全管控水平,還實現了資源優化調度和有效管理。
來到工廠中控室,《中國冶金報》記者只見大屏駕駛艙系統將項目中重點數據以儀表盤、曲線圖、柱狀圖等可視化方式動態展示,方便工作人員實時觀察設備運行狀態、環保檢測等各種參數的變化,項目狀況一目了然。
“我們還研發了設備狀態監控的故障預測、微檢修、VR(虛擬現實)檢修、人員定位健康監控等系統,有效實現了對人和物的安全進行分析、評估、預防、規避,大幅提高了安全生產水平。”程勇介紹。

圖為數字巡檢
《中國冶金報》記者發現,廠區里幾乎看不到忙碌的工人,安全員只需戴上VR眼鏡就能“云到達”車間,化身“數字巡檢員”,不一會便可完成全廠區安全檢查,省時省力又方便。
工廠建設的工業物聯網有了5G等技術鏈接,實現了各層級資源間的信息交互,在數據匯集基礎上,永鋼還開發了MES(數字化制造執行系統)、質量管理、設備管理等系統,并覆蓋工廠生產制造全過程,推動工序能耗穩步下降至設計水平的70.7%。
5G全連接工廠實現了網絡化的監督管理制度,進一步增強安全保障,讓生產運營更有前瞻性和協同性。單個生產環節的數據通過智能采集,與工廠網絡全部打通,克服了孤島式、單工序“單打獨斗”的問題解決模式。
“接下來,永鋼將利用云計算、大數據、AR等先進技術,讓更多5G應用成為生產運營的加速器,賦能企業高質量發展。”程勇表示。
“我們的總體目標是基于數字化轉型,實現‘跨產業、跨要素、跨界面、跨空間’的融合與協同,同時以利潤增長為中心,以效率、效益為根本,成本持續降低、效率持續提升、風險持續可控、數據持續變現、健康持續順行、市場持續增長,促進競爭力持續提升。”吳毅說道。
甩掉傳統標簽,打造“智造”名片。通過智能化改造、數字化轉型,永鋼把互聯網、大數據等新技術與生產制造、管理機制進行深度融合,走出了一條以信息化帶動工業化、以工業化促進信息化的新型工業化道路。
智慧鋼廠,就是永鋼模樣。